Real-life Case Studies - How They Implemented Their Universal Robot With Success
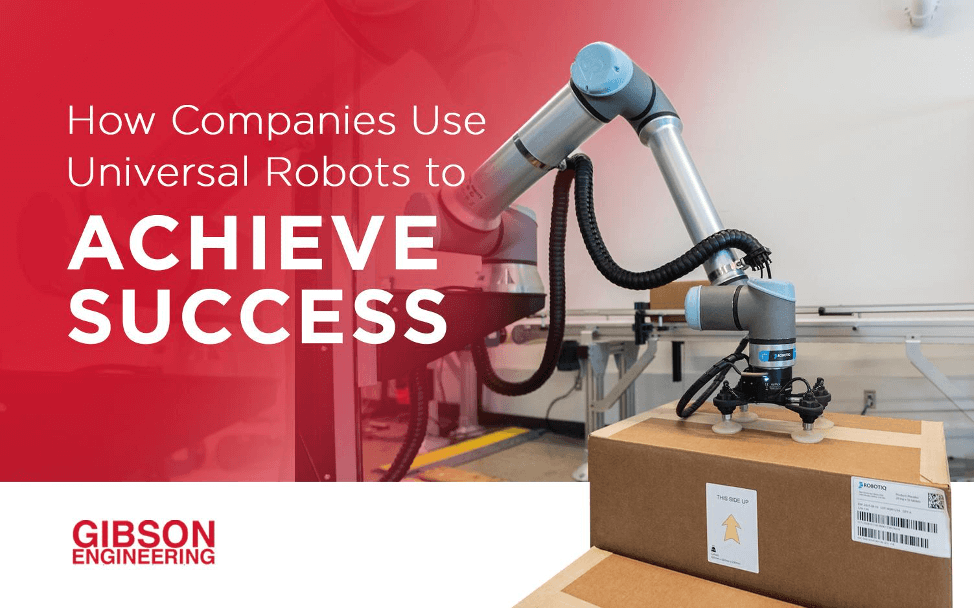
Automation is no longer reserved only for the biggest players in the manufacturing industries. Thanks to collaborative robots, SMEs can now leverage the power of automation to expedite manufacturing processes, reduce errors, and reduce operational costs.
Collaborative robots are quite versatile. They are durable, can be easily programmed, and can automate various processes on the production line. Read the following case studies to assess whether the value cobots deliver is the one that can benefit your operation.
Darex - Universal Robots Optimize Assembly and Packaging by 30%
Darex is based in Ashland, Oregon. It is a family-owned company that specializes in making drill and knife sharpeners. It features fast-paced production lines. Many of the tasks are repetitive, and they take a toll on the workers, reducing productivity and efficiency.
The company decided to look into automation because they add more and more new products to the product line each year. The limiting factors are the space and number of employees. Both these factors make it challenging for the company to maintain the same level of capacity.
Darex operates in quite a competitive niche. Hiring more people or expanding would increase the production costs and make the company less competitive. It made the company owner start looking into Universal Robots solutions. They appeared easy to program, affordable, and collaborative. Being able to have people work next to the robots appeared very attractive to the company.
Darex decided to install Universal Robots to automate two processes:
- Screwdriving
- Box erecting
Before implementing Universal Robots, human operators had to screw drive using a pneumatic screw gun manually. Given that it is a repetitive task, there were a lot of errors. More specifically, the quality issues arose from missing screws. The robot successfully took over and handled the task with no errors.
After the first successful implementation of the Universal Robots solution, Darex moved on to adding the conveyor system, PLC controlling, and another robot in charge of box erecting. Box erecting is a complex process:
- Grab a box out of a cassette;
- Fold it into shape;
- Set it into a staging platform;
- Grab four individual cartons;
- Load the case;
- Close the lid and push it through the taping station;
- Check-weighing conveyor checks whether the case weighs the right amount;
- If a case doesn’t weigh the right amount, the check station signals the boxing robot;
- The boxing robot takes that case and sets it aside.
Nevertheless, the engineers had no problems programming the collaborative robots and had them execute this task error-free.
The benefits of using universal robots were:
- 27 to 30% more efficiency;
- More agile workforce;
- ROI is achieved in slightly less than a year.
Aircraft Tooling Inc. - Universal Robots Work Reliably in Extreme Environments
Aircraft Tooling Inc. is a small aviation repair company located in Dallas, Texas. The company specializes in thermal and plasma spray for commercial airliners. The plasma and metal spray processes of parts were long overdue for automation. The application process is quite hot and dusty, making it hard for the employees to work.
The company started looking into automation solutions. Universal Robots came up as viable solutions. These collaborative robots work reliably in extreme environments with flammable and poisonous chemicals. The company had high requirements a robot would have to meet to be considered for installation:
- Work-friendly;
- Proper weight and payload;
- Affordable cost.
The most important requirement for a robot was to be able to execute and withstand tasks in a hot, toxic, and dusty environment.
After thorough market research, Aircraft Tooling Inc. decided to use Universal Robots. More specifically, the UR10. The plan was to install the robot to handle the High-Velocity Oxygen Fuel (HVOF) process. These processes are done under scorching temperatures. UR10 had to endure a really hot plasma gun with considerable recoil. It managed to withstand the harsh environment while completing the task successfully.
In this case, Universal Robots solution appeared not only versatile but durable. It requires little to no maintenance. To continue to use it, all the operators needed to do is dust it off and clean it.
Universal Robots delivered the following benefits to Aircraft Tooling Inc.:
- Easy installation;
- Affordability;
- Less than 4 hours from unpacking to being fully operational;
- Great durability;
- High-precision work;
- No downtime over the course of 3 years, aside from regular maintenance and cleaning.
Montana Solar - Workforce Freed up for More Value-added Tasks
Montana Solar specializes in designing and installing mounting solutions for solar modules. The company is based in Helena, Montana. Every summer, the company experiences a 300% increase in demand. It puts strain on the workforce as MT Solar is unable to find skilled workers. The lead times increased and were up to three times longer than they were supposed to be.
The company started looking for an automation solution that could fit in their production line. The robots had to be very flexible because MT Solar makes a wide range of mounting parts. Conventional automation solutions were out of the question due to the high prices and complicated programming and setup.
After thorough market research, MT Solar decided to go with Universal Robots. Easy installation and the ability to work alongside the robots were two main factors that affected this decision. Today, Universal Robots at MT Solar autonomously run a complete MIG welding cycle, welding six to eight parts in each cycle. MT Solar identified the following key value drivers for adopting Universal Robots:
- Employees are freed up and available for other tasks
- Improved quality of products
- Collaborative and safe
- Able to meet 300% seasonal increase in demand
- Completely automated high mix/low volume production
- Low maintenance
- Easy troubleshooting
These three cobot case studies outline the unique use cases and the capabilities of Universal Robots. As you can see, collaborative robots can help you automate highly complicated and industry-specific processes. They are also built with durability in mind so that you can use them even in harsh environments.
If you want to automate a task or discover which tasks you can benefit the most from automating, feel free to contact Gibson Engineering. Talk with a professional automation engineer to take your production floor to the next level.