The Gibson Robot Lab
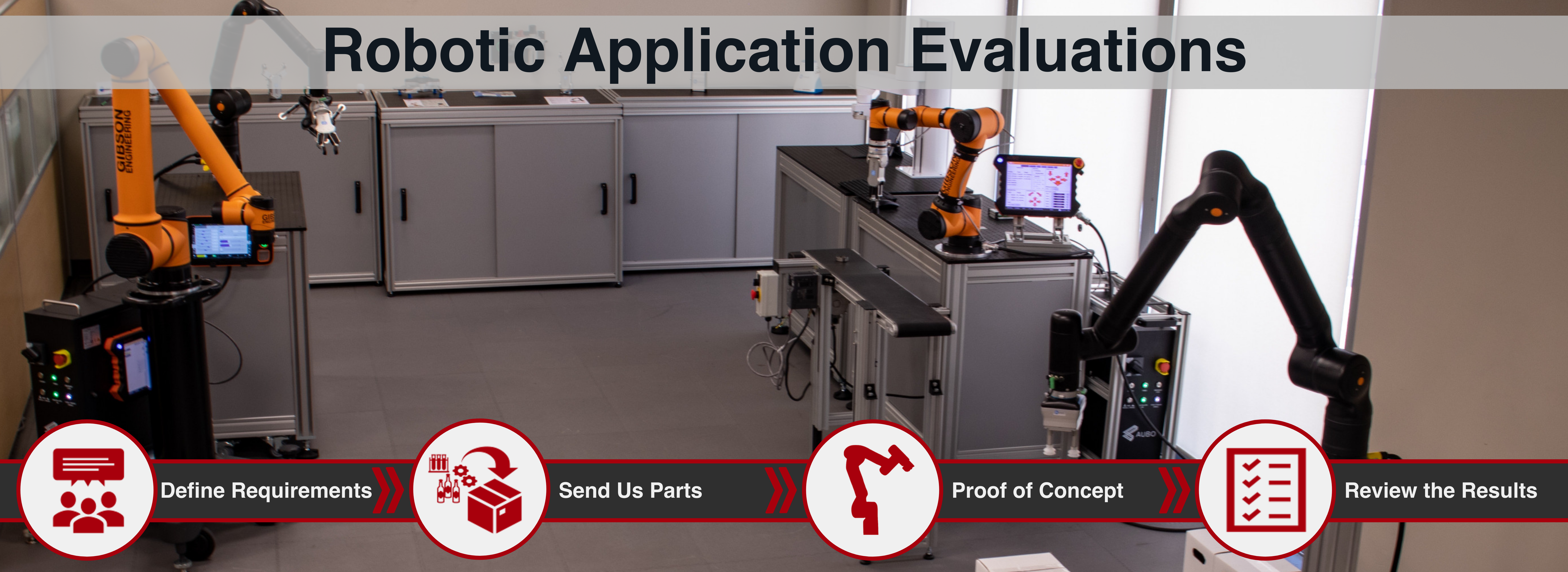
Gibson Engineering combines our extensive experience in robotics and our state of the art robotics lab to help provide you the confidence to move projects forward. Our team of application engineers is available to provide you real data to determine the feasibility of robotic applications. We will perform physical proof of concept testing in our lab with your parts or run the software simulations to help you understand capability and challenges with part handling, locating, and cycle times specific to your application. Contact us today to get started or learn more about how we can help you be more productive.
Our Robotic Technologies
Robot Product Solutions
Robotic Application Evaluation Process
Gibson Engineering can test the feasibility and functionality of your next robot application to get projects running quickly, safely, & efficiently. Our team of experienced professionals can identify ways your automation project can be made more productive or cost-efficient through extensive lab testing and industry experience while minimizing risk.
Gibson Engineering uses a simple, efficient system for an effective robotic application evaluation every time, applying four steps to assess everything from your end-of-arm tooling (EOAT) requirements to ways of presenting, orientating, or feeding parts/materials.
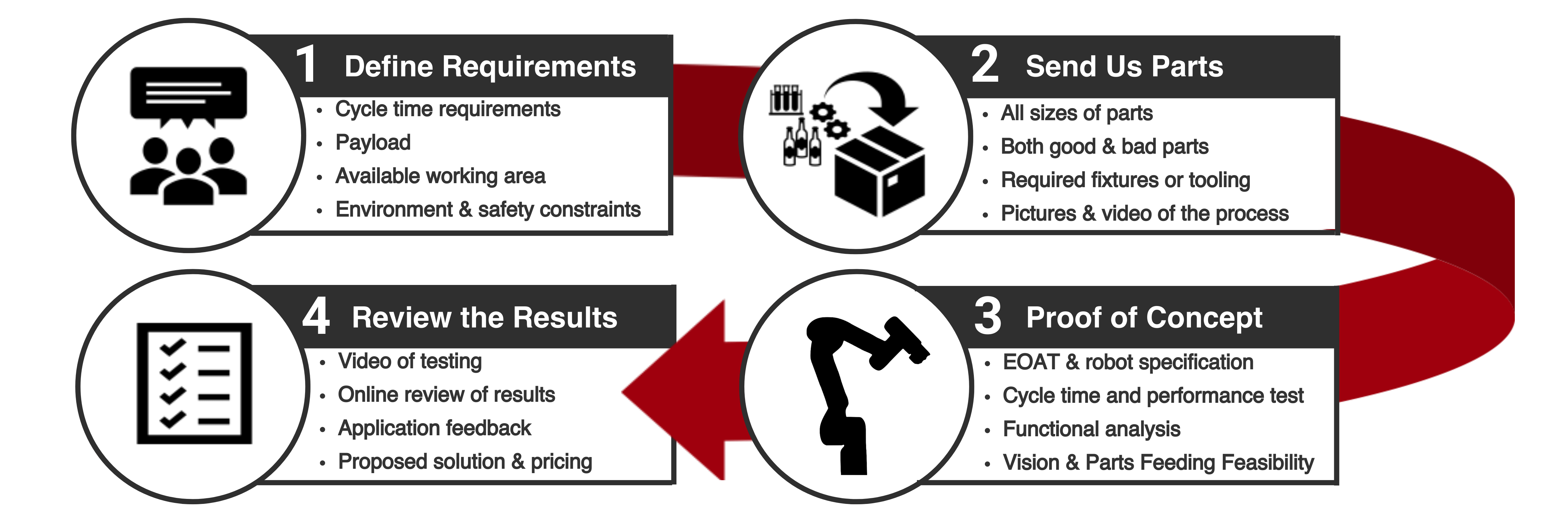
1. Define Requirements
The first step is to define the requirements of your robotic system. Determining what your robot needs to accomplish in your automation application allows the Gibson Engineering robot lab to make more discerning & accurate recommendations for a potential solution.
- Cycle time requirements: Consider the amount of work/travel your robot needs to complete in one cycle and determine how much time it needs.
- Payload: Identify the intended function of your robot and what parts/material are being moved.
- Available working area: Determine the dimensions of the working space for your industrial robotic arm.
- Environment and safety concerns: Evaluate all environmental and safety concerns to ensure a secure and reliable robotic operation.
2. Send Us Parts
The next step in a robot feasibility study is to send the Gibson Engineering team any sample parts from your application, both good and bad parts in all sizes, to make evaluations as "real world" as possible.
You should also submit any required fixtures or tooling, as well as pictures or videos of how the process works. These things are crucial for a successful evaluation, as they allow our team to recreate the application requirements accurately and get a thorough understanding of the process.
3. Proof of Concept
This step reinforces the functionality and abilities of your robot. Gibson Engineering will determine the end-of-arm tooling needs and robot specifications. We will also include a functional analysis of the robot, complete with the cycle time and performance tests.
Additionally, Gibson Engineering will provide feedback on vision and parts feeding feasibility.
4. Review the Results
In the last stage, once requirements & samples have been gathered, the application can be physically set up & tested in the Gibson Engineering robot lab. Our team of engineers will get back to you with detailed notes and suggestions on what robot, gripper, part feeding system etc is optimal for your application.
This step will include several key components, including:
- Video of testing
- In-person or online review of results
- Application feedback & recommendations
- Proposed solution and pricing
Robot Training Through Gibson
Learn more about our classroom-based training on Robotic Products:
Lean More Today From Gibson Engineering
Gibson Engineering is a top-tier solutions provider for leading manufacturers of industrial automation products. We offer custom solutions to optimize your company's operations, saving you time and money through more efficient and cost-effective processes. Our highly skilled and experienced engineers can deliver solutions to numerous industries in machine control, machine safeguarding, motion control, pneumatics, robotics, machine framing, sensors and more.
For more than six decades, we've committed ourselves to going the extra mile to help our clients succeed. Our mission is to expand your company by increasing your productivity, profitability and competitiveness.
Get in touch with one of our experts online to learn more or request a quote today to get started.
Read our latest Robotic Articles
See our most recent publications from the Gibson specialists about robotic technologies and applications