Industrial Robot Safety Standards and Tips
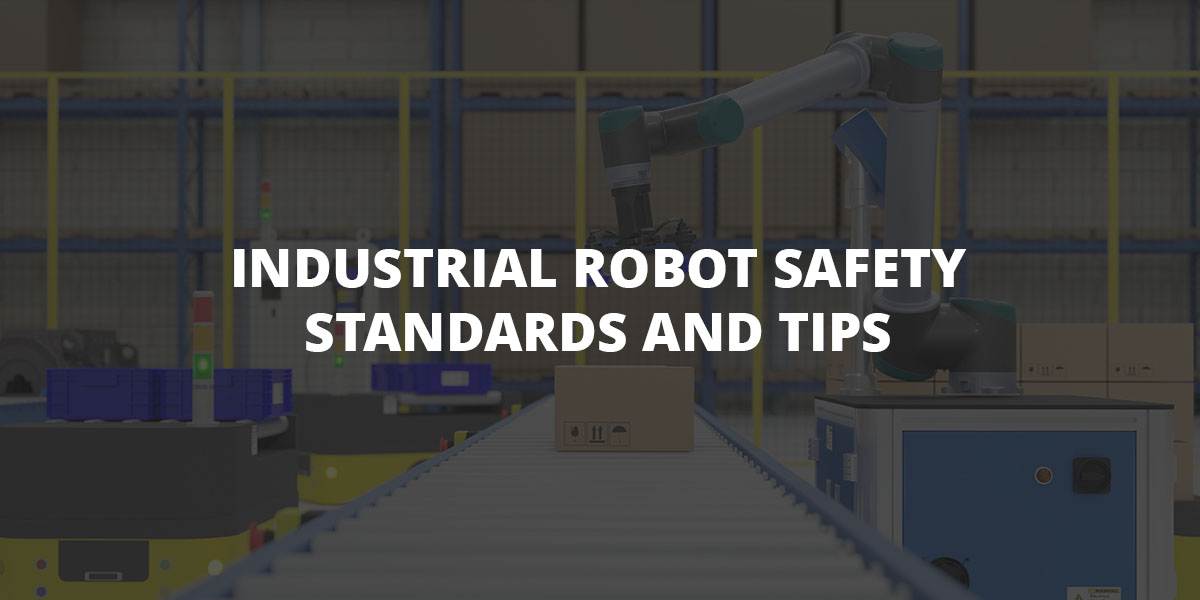
There's a significant increase in the adoption of industrial robotic systems to mitigate labor shortages and boost productivity in the manufacturing industry. Robots' appeal also stems from their ability to increase worker safety. According to a 2020 study, adopting robots has reduced up to 16% of work-related injuries.
However, manufacturers and operators must take specific precautions to mitigate these automated systems' hazards and risks. Below, we will highlight industrial robotics safety standards that ensure their safe operations and reduce the risk of harm to human workers. We also share several solutions to stay compliant with the guidelines.
Safety Standards for Manufacturers and Operators
The following are some noteworthy industrial robot safety standards that manufacturers and robot operators in all industries must adhere to. These conventions ensure reliable robot performance and human worker safety.
- ANSI B11.19:This standard defines the performance requirements for the design, construction, installation, operation and maintenance of machines, including power-driven industrial robots, to reduce risks and hazards.
- ISO 10218: The ISO 10218 parts 1 and 2 stipulate the safety requirements for industrial robots. It seeks to manage dangerous circumstances by identifying deficiencies in the design, installation, control and operation of new and existing robots and robotic devices.
- ISO 13849: ISO 13849-1:2015 provides safety guidelines for testing and validating the design and operation of safety-related parts of control systems. The standard dictates the controls to mitigate the robot's risk and failure rates.
- OSHA 1910.147 Subpart J: The OSHA 1910.147 Subpart J standard dictates that employers should install suitable logout and tagout devices to energy-isolating devices such as robots to curb sudden energization that could cause injury to workers.
- ANSI/RIA R15.08: Part 1 of the ANSI/RIA R15.08 standard specifies the primary hazards of using mobile robots in industrial environments to enhance human workers' safety.
Solutions to Enhance Industrial Robot Safety
When humans work alongside robots, their security is a priority. While robot manufacturers implement machine safety controls, such as interlocks, emergency stop buttons and sensors, employers are responsible for adding extra safety mechanisms to keep workers safe around the robots. The following tips and products will help you improve workplace safety by enhancing how your team members interact with the robots.
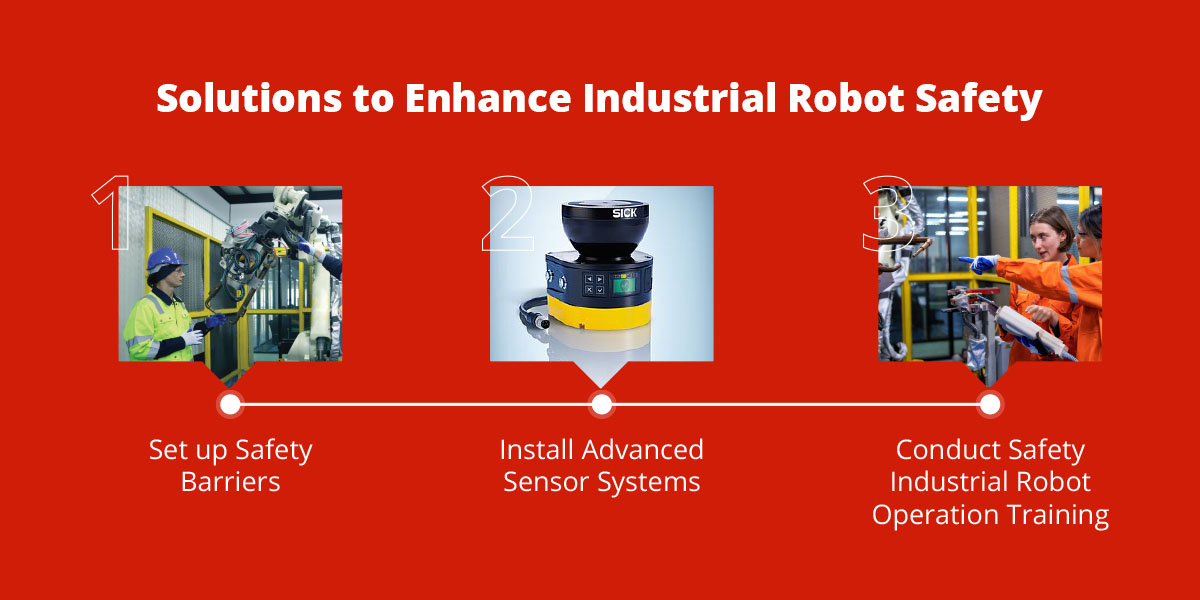
Set up Safety Barriers
Installing physical barriers in areas where industrial robot systems operate limits access to humans and mitigates other hazards posed by operating machines. As a result, physical barriers lower the risk of collisions, interaction with other hazards and, ultimately, injuries at your workplace. You can implement various physical barriers in your industrial facility.
- Guards: Rigid safety guard fences protect the employees working around the robot cells by keeping people out of where industrial robots operate. Robotunits safety fence systems are sturdy enough to ensure robots don't break through the barrier. They're also prefabricated and fully customizable to meet your unique needs.
- Shields: These safety barriers protect human workers by confining the machines and other hazards such as debris, dust, smoke, fumes, mist and arc glare.
- Awareness barriers: These warn human workers of impending danger and hazards when approaching an industrial robot system.
Safety light curtains are examples of non-separating barriers that detect the presence of humans in or near the robot cells and slow the robots down to prevent injury. SICK has various light curtains in different sizes and resistance variants to block off hazardous robot operation areas. The deTec4 light curtain provides intelligent protection to enhance productivity with muting and innovative presence detection features.
Machine safeguarding barriers such as laser guides, lockout and tagout procedures also enhance safety by locking robot parts when employees conduct non-routine tasks.
Install Advanced Sensor Systems
Safety sensors are crucial for detecting the presence of humans and objects in the robot cells. The best sensors communicate with the robot's control systems to activate appropriate safety measures, such as slowing down or stopping to prevent collisions and ensure a safe working environment. Different types of sensor systems, including laser scanners and proximity sensors, provide real-time assessments of any obstacles in the way of the robots.
The microScan3 is a reliable safety laser scanner from SICK that uses an innovative safeHDDM scan technology to scan and detect people and objects near robots. It boasts an extensive range, precision measurement data and high resistance to ambient light, dirt, dust and other scanners. It also complies with international robot safety standards and easily integrates into existing robot systems.
The microscan3's compact and rugged design ensures stable manufacturing processes, efficient machine design and uninterrupted production. The smart connectivity feature lets you enjoy fast, flexible installation and safe communication, ensuring you can integrate any microScan3 device into unlimited networks.
Conduct Safety Industrial Robot Operation Training
Robot operation training is another way to prevent accidents and injuries among your personnel. Highly trained robot operators also maximize the return on investment for your automated systems and safety equipment by ensuring the robot systems maintain peak productivity and reduce downtimes. All operators must understand how machine and safety advancements work.
You can further reduce user error by having open lines of communication with personnel. Remind them of post-safety rules, such as removing all obstructions from robot work areas and how to access machine lockout and tagout procedures.
Gibson Engineering offers beginner and advanced robot training classes to help you achieve your automation goals. Our customized courses equip your staff with hands-on skills. Besides hands-on training, we also conduct regional seminars throughout the Northeast.
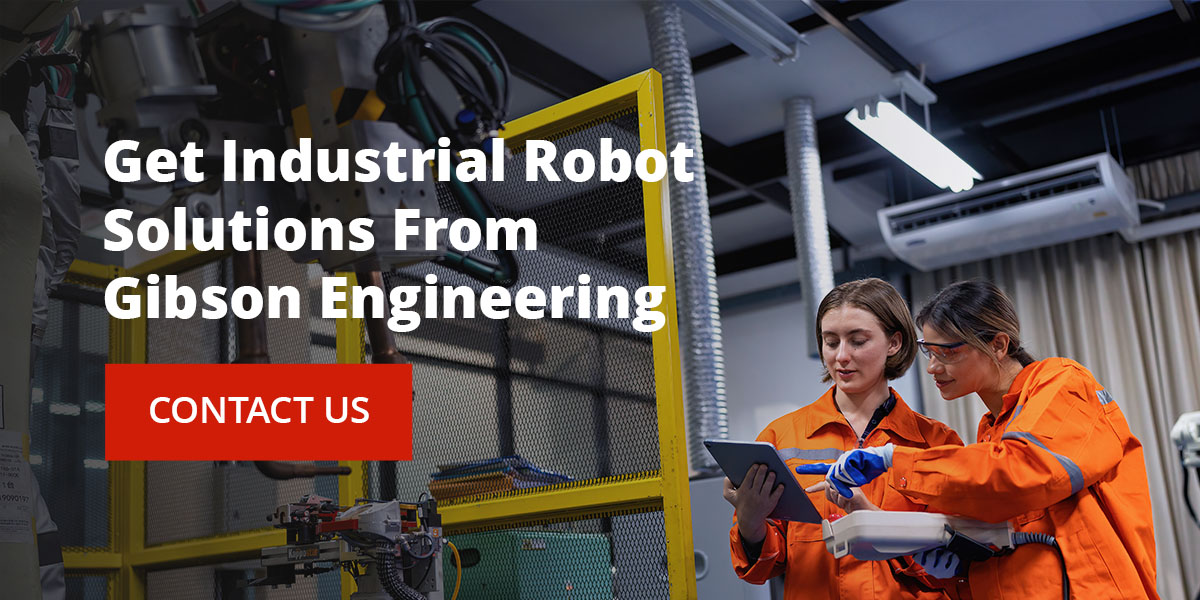
Get Industrial Robot Solutions From Gibson Engineering
Machine automation and robotics in manufacturing and other industries can improve productivity, efficiency and worker safety. However, plant owners must prioritize and invest in advanced technology. At Gibson Engineering, we provide manufacturers with custom safety solutions for operating industrial robotic systems.
We distribute world-class SICK sensing and machine safety technologies and Robotunits safety fencing, machine frames and guards to reduce the risk of workplace injuries. Contact us today to order or learn more about how we can help you enhance industrial robot safety.